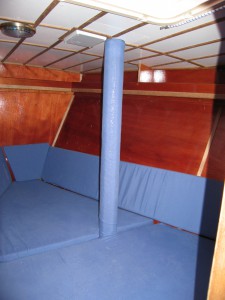
Was nicht so gut gefiel, war die Gestaltung des Vorschiffs, die hier im Bild zu sehen ist. Die Ankerkette lief mitten durch die Kabine und machte diese quasi unbrauchbar. Der Ankerkettenkasten lenzte einfach in die Bilge, so dass diese ständig feucht war. Die horizontale Ankerwinsch wurde daher durch eine vertikale ersetzt und die Ankerkette wird jetzt im Ankerkasten vor der Vorschiffskabine gestaut. Dadurch konnte der 40 kg schwere Ankerkasten aus dem Vorschiff entfernt werden, was die nachteilige Gewichtsverschiebung zum Bug wieder ausgleicht. Das gesamte Lenzsystem der Aloma haben wir überarbeitet, da auch die anderen Bilgen immer feucht waren. Die im Schiff verteilten Bilgepumpen waren einfach auf den Rumpf geklebt und mit Rückschlagventilen versehen worden, die natürlich nie richtig dicht sind. Wenn dann die Grauwasserpumpe ins gleiche System pumpt, ist die Überschwemmung vorprogrammiert. Durch die Verklebung der Bilgepumpen kam es in der sauerstoffarmen Umgebung zu einer verstärkten Korrosion. Im Motorraum hatten sich unter der Pumpe schon Pittings im Aluminium gebildet. Überhaupt der Motorraum, hier war ein 80 Liter Warmwasserboiler und der Kompressor der Klimaanlage installiert, die nur mit ausreichend Landstrom betrieben werden konnte. Beides wurde umgehend entsorgt.
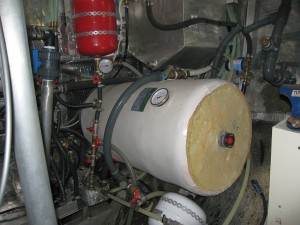
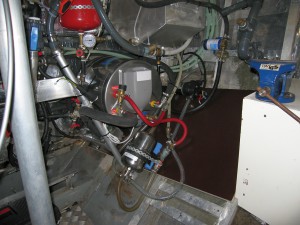
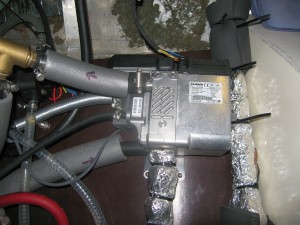
Der neue Boiler hat 24 Liter Inhalt und außerdem haben wir eine Heizung mit Wasserkreislauf eingebaut. Die Wärme wird über sehr leichte Alu-Heizkörper und zusätzliche Heizgebläse im Boot verteilt. Der Boiler ist ebenfalls in den Heizkreislauf eingebunden. Außerdem ist der Heizkreislauf über einen Plattenwärmetauscher mit dem Kühlwasserkreislauf der Antriebsmaschine gekoppelt.
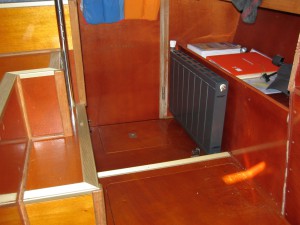
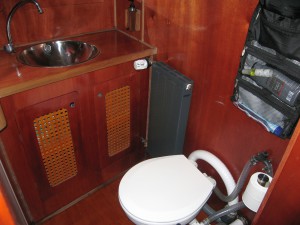
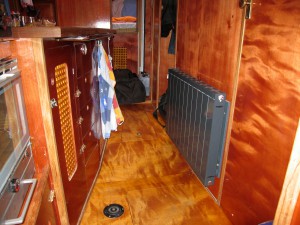
Dann gab es da noch ein Isolationsproblem. Schon im ersten Winter lief das Kondenswasser bei Lage aus den Kabinendecken. Der deutsche Vorbesitzer, Betreiber einer spanischen Firma für Klima und Kältetechnik, hat die 40 mm dicke Polystyroldämmung nicht flächig verklebt und Stromkabel bevorzugt zwischen Isolierung und Alu-Rumpf verlegt. Die Isolierung wurde daher von uns über die Jahre erneuert. Hierzu war mehr oder weniger die vollständige Entkernung der Kabinen notwendig.
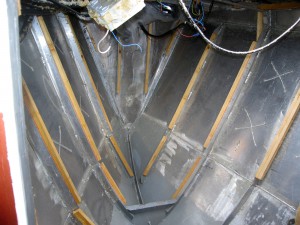
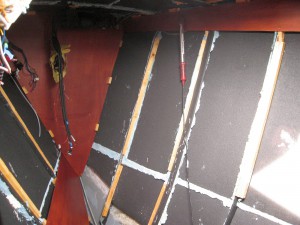
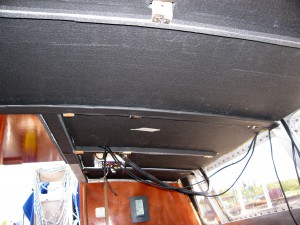
Wir haben 40 mm dicke Trocellen Platten (geschlossenporiger PE-Schaum) verwendet, die wir flächig verklebt haben. Um Kondenswasser zu vermeiden, sind die Spanten mit 3 mm Armaflex Isolierung beklebt. Lücken wurden dann mit PU-Schaum ausgespritzt.
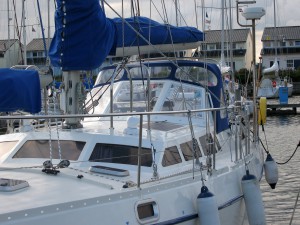
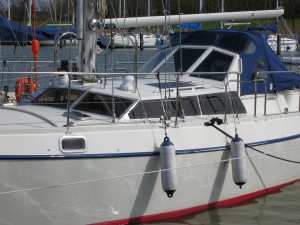
Die 15 mm dicken Acrylglasscheiben hat die Werft Nereide Yachting von innen montiert. Als Dichtmittel wurde die vom Konstrukteur Kurt Reinke empfohlene Fako-Binde benutzt. Diese plastische Dichtung setzt sich mit der Zeit, drückt sich seitlich unschön heraus und die Schrauben müssen nachgezogen werden. Dies war jedoch nicht möglich, da über die versenkten Schraubenköpfe lakiert wurde. Die Scheiben waren folglich undicht. Außerdem empfanden wir die innen montierten Scheiben als Risiko bei Wasserschlag. Wir haben alle Scheiben demontiert, neu zugeschnitten, gephast, poliert und von außen montiert. Als Dichtung wurde ein 4 mm starkes Band aus EPDM-Zellkautschuk mit einseitigem Montagekleber verwendet. Auf die Dichte achten! Die aufgrund einer Fehlberatung zunächst verwendete Streifenware mit 70 kg/m³ Dichte mussten wir wieder entfernen und durch Plattenware mit 140 kg/m³ Dichte ersetzen.
Beim Innenausbau in Spanien wurden bevorzugt verzinkte Spax-Schrauben verwendet, die teilweise schon beim Bootskauf rostig aussahen. Inzwischen haben wir tausende Schrauben gegen ihre VA-Version getauscht. Das kostet alles Geld und Zeit, Zeit, Zeit.
In Bearbeitung, Fortsetzung folgt!
Die elektrische Installation stellte sich ebenfalls als abenteuerlich heraus und das trotz CE-Zertifizierung. Mehr dazu findet ihr im Kapitel Elektrik.